プラスチックの基礎知識
プラスチックの特徴
プラスチックとは、英語で「可塑(plastic)」という意味があり、熱を加えると変形する性質を持っています。そのため、成型加工がしやすく、透明性があり着色も自由にできます。また、電気的絶縁性や断熱性もあり、大量生産もできるので、プラスチックの製品はさまざまな分野で利用されています。
プラスチックは石油から作られる
プラスチックは、石油から作り出されます。油田から採れた原油を石油精製工場で分留し、ガソリンやナフサ、灯油、軽油、重油などの成分に分離させます。分離された成分のうち、「ナフサ」がプラスチックの原料になります。そしてナフサに熱を加えることでエチレン、プロピレン、ベンゼンといったプラスチックの原料になる「モノマー」が作られます。モノマーはその後ポリマーという「高分子化合物」に変化し、ペレット材料として製品加工に使用されます。
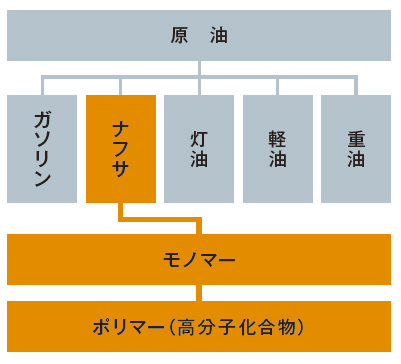
プラスチックの分類
プラスチックは、大きく「熱可塑性プラスチック」と「熱硬化性プラスチック」という2つの種類に分けられます。
熱可塑性プラスチックは熱を加えると溶けて柔らかくなり、型に入れて冷やすと固まって製品になります。また、一度合成したプラスチックjは、再利用できます。逆に熱硬化性プラスチックは、熱を加えても柔らかくならず硬くなります。そして一度硬化すると、基本的には熱を加えても再び柔らかくならない性質を持っています。
-
熱可塑性プラスチック
・熱を加えると溶けて柔らかくなる
・冷やすと固まる
・再利用できる -
熱硬化性プラスチック
・熱を加えると硬くなる
・一度硬化すると熱を加えても硬いままである
プラスチックの種類
プラスチックは「汎用プラスチック」と「エンジニアリングプラスチック」にも分けられます。
汎用プラスチックは、高性能ではなく価格も比較的安いのが特長です。耐熱温度は100℃程度で溶解するものが多いため機構部品の素材として用いると精度が保てない場合もあります。ポリエチレン(PE)、ポリプロピレン(PP)、塩化ビニール樹脂(PVC)、ポリスチレン(PS)が代表的な汎用プラスチックになります。
エンジニアリングプラスチック(エンプラ)とは、汎用プラスチックと比べて耐熱温度や機械的強度を高めたプラスチックです。一般的に、耐熱温度が100℃以上あり、強度が50MPa以上、曲げ弾性率が2.4GPa以上あるプラスチックを「汎用エンジニアリングプラスチック(汎用エンプラ)」と呼んでいます。さらに、150℃以上の高温でも使用できるものは、「スーパーエンジニアリングプラスチック(スーパーエンプラ)」と呼ばれています。代表的なエンプラは、ポリカーボネート(PC)、ポリアミオド(PA)になります。
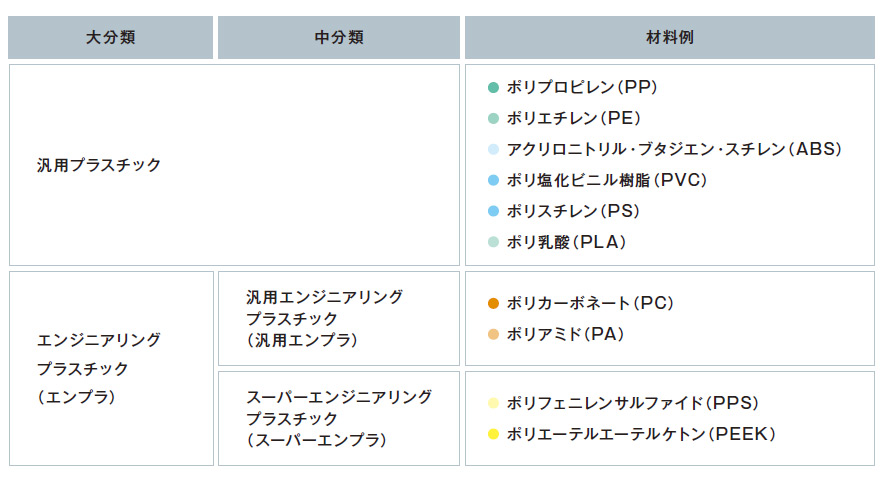
プラスチック別「耐熱性」と「引張り強度」の比較
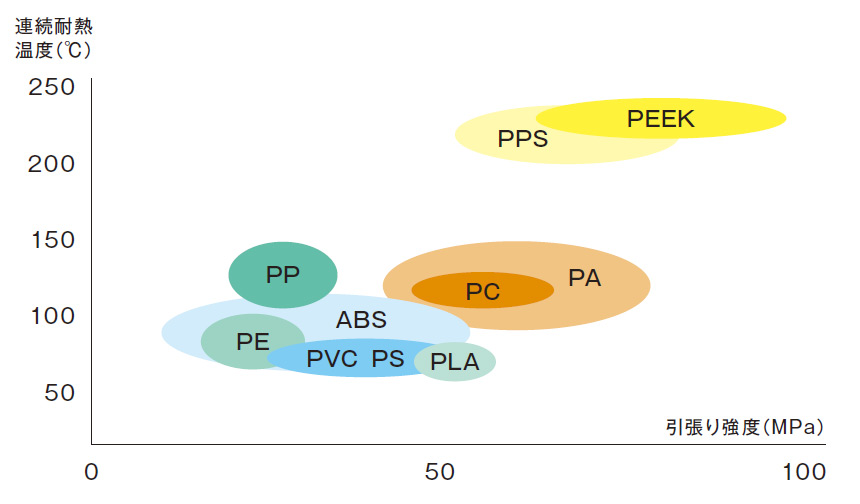
-
引張り強度
試験片をはさみ荷重を加えることで、応力とひずみとの関係を測定して引張り強さを求めます。試験は専用の引張り試験機を使っておこないます。
-
連続耐熱温度
一定の温度の中に40,000時間放置し、その性質が初期の50%劣化した温度を「連続耐熱温度」といいます。
プラスチックの成形方法
プラスチックの成形方法はいくつか種類があります。
それぞれの成形方法には特長があり、対象物や使用目的などによって使い分けられます。
プラスチックの成形方法とその特長
成形方法 | 対象物 | 特長 |
(1)切削加工 | 半導体製造装置部品、電子機器部品、医療機器、治具など多種多様な製品 | 小ロット、多品種向け |
(2)射出成形 | 自動車部品や電化製品など日常的に使用するあらゆる製品 | 大ロット、高品質向け |
(3)ブロー成形 | ペットボトル、シャンプーボトルやポリ袋など | 単純な形状向け |
(4)押出成形 | パイプ、建材など | 同形状の大量生産向け |
(5)真空中型 | 形状確認、営業用サンプルなど | 試作製作向け |
(6)3Dプリンタ | 切削や射出成形で製作できないもの(中空形状など)を含むあらゆる製品 | 試作製作向け |
(1)切削加工
-
切削加工とは、切削工具で切り削る加工方法です。
切削方法には、施削・穴あけ・中ぐり・フライス削り・研削・歯切り・放電加工・レーザー加工といった方法があり、それぞれの切削特長をもった工作機械が存在します。工作機械の中でもマシニングセンタは、多種類の加工を連続でおこなえます。小ロット多品種、高い精度が必要な製品生産に向いていて、多種多様な製品を作れます。
(2)射出成形
射出成形は、プラスチック製品を製造する「代表的な成形方法」です。
射出成形機は、プラスチック原料を溶かし金型へ流し込む「射出装置」と、プラスチックを固め製品を取り出す「型締め装置」の2つに分かれます。
使用される金型は、高圧な圧力に耐える力が必要(1㎠あたり200~700kgほど)で、少しでも寸法が違うと、装置全体へかかる圧力が大幅に変わってしまうため高い精度が必要です。そのため、金型製作が高額になるので、小ロットの生産には適していません。
射出成形は3Dプリンタと比較されることが多いですが、製造スピードと精度では射出成型が圧倒的に勝ります。
自動車部品や電化製品など日常的に使用するあらゆる製品が作られています。
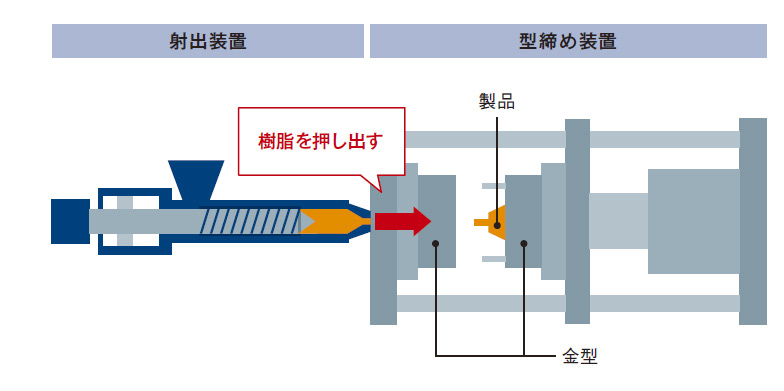
(3)ブロー成形
ブロー成形も射出成形と同様に生産性の高いプラスチック成形方法です。
バリソンと呼ばれる小さい筒状のプラスチック容器をエアーで膨らませます。そして、膨らませたプラスチック金型で固定し、冷却してから固まったものを取り出します。射出成形と成形の流れは同じですが、ブロー成形では、射出成形ほどの強度・精密さを必要としません。ペットボトル、シャンプーボトルやポリ袋などが作られます。
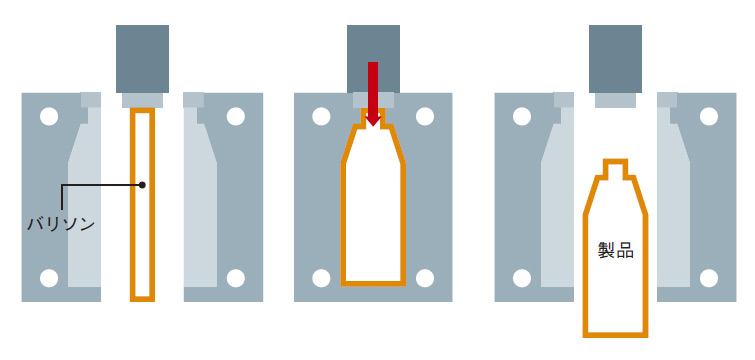
(4)押出成形
押出成形は、溶かしたプラスチックを「ところてん」のように金型から押し出すことによって断面を形成する方法です。そのため、金太郎飴のようにどこを切っても同じ形状のものを長く作るのに適しています。
プラスチックや金属材料その他、色々な材料の製品が作られています。
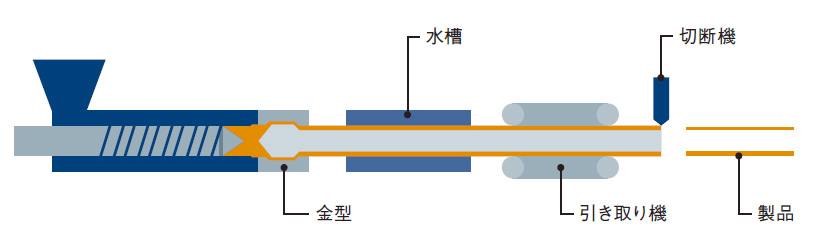
(5)真空注型
真空注型とは、樹脂をシリコンゴムで作られた型に流し込み、成形する加工方法です。
まずは、マスターモデルの型を作り、複製品を作ります。
真空注型は、1週間程度の納期で複製の試作モデルを製作できます。金型を使用する場合と違い、設計変更にも柔軟に対応できるのが特長です。利用できる材料はウレタン系樹脂などに特定されます。
真空注型は大量製品に向いていませんが、金型製作のように高額な費用をかけずに、高精度の樹脂製品を作ることができます。そのため、試作品製作などに利用されています。
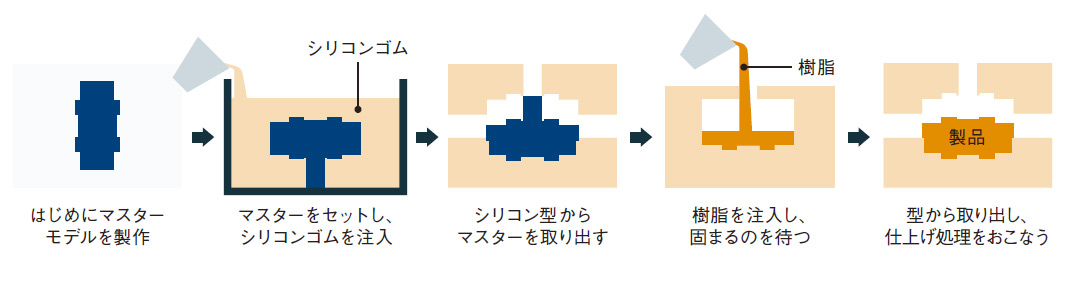
(6)3Dプリンタ
3Dプリンタは、コンピュータ上で作った3Dデータを基に、その断面形状を積層して立体物を作成します。インクジェットヘッドからUV硬化樹脂を吐出しながら造形するインクジェット方式、熱で溶かした樹脂を少しずつ積み重ねていくFDM方式、粉末の樹脂に接着剤を吹きつけていく粉末固着方式などの方法があります。
近年、急速に普及が進む3Dプリンタは、主に商品開発の試作品の製作で利用が進んでいます。
試作時における成形方法の比較
製品開発時の試作品を製作する主な成形方法として「切削加工」「射出成形」「3Dプリンタ」があります。
(1)切削加工による試作
切削加工は試作品製作において最も利用されてきた成形方法です。実際の製品と同じ材料で精度よく製作ができます。しかし、1つあたりのコストが高く、外注する場合製品のサイズや複雑さに依存しますが、1週間以上の納期が必要となります。
(2)射出成形による試作
射出成形で試作品製作をおこなう場合、アルミ材などを使用した簡易金型と呼ばれる金型強度やコストを下げた金型で製作されます。さまざまな材料の製品を作ることができ、実際の製品に最も近い性能を出せます。しかし、コストや納期は、切削や3Dプリンタと比較して大幅に劣ります。
(3)3Dプリンタによる試作
3Dプリンタによる試作は、切削加工や射出成形と比べて低コスト・短納期であることがメリットです。金型を製作する必要がなく、デザインの検証を簡単に行えます。ただし、製作物によっては、造形物の強度や気密性が低く使えません。切削加工や射出成形と比べると精度と強度の面で劣ります。
以上のように、どの成形方法にも一長一短があり、設計の各プロセスで上手な使い分けが必要となります。一般的には3Dプリンタは、開発プロセスの初期段階における、デザイン性、組み付け性、部品の干渉や動作確認などで活用されます。そして、開発プロセス中盤では、液体や気体などの流体実験、放熱性の実験などで活用し成功しているメーカーもあります。一方、切削加工や射出成形は、設計の中盤から後半にかけて、実際の製品と同じ材料、同じ生産方式によって得られる試作品で、量産品と同等の評価をおこなったり、成形性(生産性)や品質のバラつきを確認したりするような活用がされています。
試作時における成形方法の比較
成形方法 | 品質 | コスト | 納期 |
切削加工 | 高い寸法精度が得られる | サイズや複雑さによって数万~数十万円 | 見積、加工プログラム作成、加工、検査などの工程が必要であり、外注した場合、5日程度~ |
射出成形 | 量産金型で製造した実際の製品と同等レベルの品質が得られる | 量産金型より安いが、小さな試作用金型でも数十万円~になる | 見積、金型製作、成形試作などの工程が必要であり、3週間程度~ |
3Dプリンタ | 積層ピッチやプリント速度の影響により実際の製品より精度が劣る | 自社で製作した場合、材料費のみ | 自社で製作した場合は1日程度~ |
3Dプリンタで利用される材料
3Dプリンタでは成形方法ごとに違う材料が使われます。どの方式も材料を積層して造形するため、強度の面では切削加工、射出成形に比べると劣る場合があります。
(1)ABS樹脂
-
機能性が高いこともあり、電気機器の筐体、建材などの広い分野で使用されています。粘着性があり、強度が高いのが特長で、サンドペーパーなどで磨くことができ、塗装もしやすい性質を持っています。3Dプリンタでは熱溶解方式で使われており、200℃以上の高温で溶かしてノズルから一筆書きで造形します。造形物は冷える過程で収縮し変形してしまうため、3Dプリンタ内部を加熱し形状を保たせるなどの対応が必要なケースがあります。また、ノズル径を小さくしにくいため、積層ピッチが0.2mm程度あり微細な造形には不向きです。
(2)PLA樹脂
-
PLA樹脂では植物性由来の成分(トウロモロコシ、ビート、イモ類mサトウキビなど)でできているため、熱溶解方式の3Dプリンタで溶かす際にも樹脂の臭いが気になりません。ABS樹脂とは違い、低い温度で溶けるために冷える過程でひずみが生じにくいのも特長の1つです。そのため、大型の造形物を作る際にも変形を気にせず作ることができます。ただし、やすりなどで処理をするのが困難で、塗装もなじみにくい性質があります。
(3)アクリル樹脂
-
合成樹脂の一種で高い透明性が特長です。また着色が容易であることから無機ガラスの代用品として建築や乗り物の窓材、照明器具のカバー、標識などに利用されることが多くあります。3Dプリンタでは、UV光による硬化速度が比較的早いためにインクジェット方式で使われます。少量の液体樹脂の状態で吐出できるので微細な造形ができるのが特長です。透明性がある樹脂で造形できるので内部の検証などに利用できます。一方で吸水率や耐熱性の問題もあるため、造形後の変形が生じる可能性があります。
(4)エポキシ樹脂
-
熱硬化性樹脂で、接着剤や塗料として利用されています。電子機器の基板やICのパッケージとして使われるのは、寸法安定性や耐薬品性、電気絶縁性が高いためです。アクリル樹脂と比較してUV光での硬化速度が遅く、光造形機の材料として使われるのが一般的です。また、UV照射を停止しても硬化反応が継続するなど扱いが難しいところがあります。一方で耐熱性や耐薬品性などの機能性が高い傾向があり、樹脂のバリエーションは多角化しやすい性質があります。
(5)ナイロン(PA・ポリアミド)
-
細かい粒子で、きめ細やかな粉末で形成されているポリアミド合成繊維の一種です。表面は少しざらつきのある多孔質の素材になります。強度がありながらも柔軟性を兼ね備えているので、曲げなどにも強い性質があります。ウィンドブレーカーなどの防寒具に使用されている他、水着や釣り糸などにも用いられます。粉末焼結方式の3Dプリンタで利用できる材料で、粉末をレーザで焼き固めて造形されます。強度があるためスナップフィットの検証に使用できます。
(6)石膏パウダー
-
粉末接着方式で用いられる材料で、石膏に接着剤を塗布して造形をする際に色も着けられるため、模型やフィギアの造形に使われます。石膏パウダーが安価なため材料費もリーズナブルです。しかし、石膏を接着剤で固めてあるだけなので、とても脆くデザインの確認以外の用途にはあまり向きません。
(7)金属
-
3Dプリンタの材料として使える金属は現状は限られた種類で、一部のSUSやチタン、銅、アルミなどが該当します。樹脂で造形する3Dプリンタは試作での利用が一般的ですが、金属造形は最終製品としての利用が見込まれます。例えば航空機では金属造形による部品の採用が積極的に行われています。一方で、量産品として使用するには、レーザで焼き固める際に熱ひずみが発生するため形状が限定されたり、造形時間がかかることが課題と言えそうです。
積層方法別の使用材料と特長
積層方法 | 特長 | 材料例 |
熱溶解積層方法 (FDM) |
ノズルから、熱可塑性の樹脂を噴射して層を造ります。安価な3Dプリンタは熱溶解積層方式が主流です。 | アクリロニトリル・ブタジエン・スチレン(ABS) ポリ乳酸(PLA) ポリカーボネート(PC) |
粉末焼結積層造形 | 粉末状の材料にレーザをあて、焼き固めて層を造ります。樹脂材料以外に金属系の材料が使用できます。 | 金属、ナイロン、ポリプロピレン(PP) |
光学造形方式 | 紫外線レーザを照射し、液体樹脂を硬化させて層を造ります。 | エポキシ樹脂 |
インクジェット方式 | ノズルから液状の紫外線硬化樹脂を噴射して、紫外線を照らすことで層を造ります。積層ピッチが細かく高精細な造形ができます。 | アクリル樹脂 |
石膏3Dプリンタ | 粉末状の石膏を硬化させて層を造ります。フルカラーの対応もできます。 | 石膏 |
高精細3Dプリンタ「アジリスタ」
(1)商品の特長
商品開発に求められる精度で、簡単に使える3Dプリンタです。
-
積層ピッチ15μm
細部まで検証できる精度
積層ピッチ15μmの高精細造形だから、デザイン確認はもちろん、部品の組み付けや機能性の確認まで幅広く使用できます。
-
水溶性サポート材
水につけておくだけ
水につけるだけでサポート材を除去できます。手間がかからず、造形モデルを誤って破損させる心配もありません。
-
オフィス仕様
特別な設備は不要です
導入するにあたって、工事や付帯設備は不要です。一般的なネットワークプリンタのようにオフィスに簡単に設置できます。
(2)樹脂特性
アジリスタの専用樹脂は設計検証に役立つ4つの特性を持っています。
-
靱性
樹脂に十分な靱性があるので、スナップフィットはもちろん薄肉の筐体のがん合も、割れの心配を低減します。
-
剛性
積層ピッチが細かいため、積層方向と垂直方向の強度にほとんど差がありません。評価しやすい樹脂特性です。
-
透明性
透明性のある樹脂なので、部品の組み付けによる干渉はもちろん、流水まで目視で確認できます。
-
形状保持性
水溶性サポート材実現のために吸水率の低い樹脂を開発しました。薄肉の形状でも変形を最小限にします。